
「3枚刃」の超硬エンドミルを市場に初めて投入!
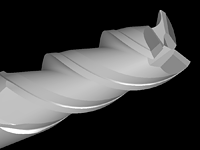
1970年代後半、金型の製造現場は、自動化・無人化による24時間生産体制の胎動期を迎えました。その過酷な使用条件に堪えられる耐久性がエンドミルにも求められはじめていたものの、市場はいまだハイス製品が95%という時代でした。
こうしたなか、日進工具では、「超硬エンドミルの時代が目前に迫っている」との認識のもと、新製品の開発に着手しました。さまざまな試作品を試していただいたエンドユーザーの声を反映させながら、約2年間かけて新製品を完成させ、1980(昭和55)年に「超硬ソリッドエンドミル」として発売しました。
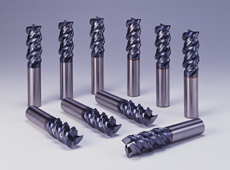
1982年には、刃数が奇数(3枚刃)の「超硬ソリッドエンドミルパワーエンドミル」の販売を開始。ハイス製に比べて高価ではあるものの、この頃になると超硬エンドミルも次第に市場に浸透し始めていました。しかし、当時、市場に出ていたものはすべて2枚刃、4枚刃という偶数刃の製品で、刃数が奇数のものは一つもなかったのです。
「パワーエンドミル」は、3枚刃の製品が主力製品の一角を占めていたこともあり、そのノウハウを用いて、短期間で3枚刃の「超硬ソリッドエンドミルパワーエンドミル」を開発できました。当初は「3枚刃は測定しにくい」という理由で思うように販売量が伸びませんでしたが、現在では、3枚刃の有用性が認められ、その生産量を増やしています。
ある開発が、小径エンドミル開拓への大きな転機に
1986年、「NHR-2超硬ソリッド深リブエンドミル」(以下、深リブエンドミル)を開発しました。金型を用いて作られる各種製品のなかでも、プラスチック製品は、特に軽量化に力が注がれており、プラスチック用金型のリブ溝は年々、細く深く、しかも複雑な構造になっていきました。
深リブエンドミルは、こうしたプラスチック用金型加工に必要不可欠な製品でした。
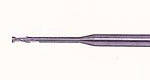
従来、プラスチック用金型のリブ溝部分の加工は、放電加工機によって行われていましたが、より効率的な加工方法を模索していたエンドユーザーから「エンドミルで加工できないものか」と相談を受けた後藤勇専務と営業担当者は、製造・開発部門に新製品の開発を依頼し、約1年の研究・試作・改良を経て、放電加工の約10分の1という短時間で、深溝リブ構造をもつプラスチック用金型を製造できる、世界初の「深リブエンドミル」を開発しました。
なお、この開発の成功は、当社がその後、小径エンドミルの市場を開拓していく大きな転機となるとともに、今日の超硬化への流れをつくるものとなりました。
当時、大手メーカーのように専任の研究開発部門をもっていなかった当社が、「深リブエンドミル」を製品化できた背景には、エンドユーザーの要望をすぐに試作できる営業と製造が直結した組織体制に加え、試作品を実際に製造現場でテストしていただけるエンドユーザーとの親密なネットワークがあったからこそです。
独自路線を選択した矢先の悲劇。復活への道へ

1990年代に入って各企業の間でCI戦略が注目されるようになり、多くの企業が社名をカタカナ表記にすることがブームとなっていました。 こうしたなか、新しい社名には、「製作所という文言を削除することによって、より幅広い事業活動の可能性を指し示すとともに、全文を漢字とすることで、技術立国日本の工具会社であること、さらにはカタカナ一色となってしまった業界のなかで、当社の独自性を主張していく」という強い意志が込められていました。
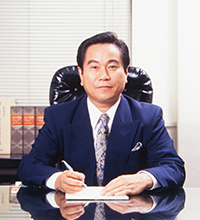
新体制がいよいよ本格的に動き出していた1991年11月、機械が24時間フル稼働していた無人の藤沢工場で火災が発生し全焼しました。幸い人的被害はありませんでしたが、同工場を中心として生産を進めていた当社にとって致命的ともいえる出来事でした。
バブル景気の末期でもあり、メインバンクやその他取引金融機関から、新工場建設計画が相次いで提案されましたが、当時の在庫状況や製品の荷動きを冷静に見つめていた社長の後藤勇は、周囲の反対を押し切り「今後、当分の間新規投資を一切行わない」という経営方針の転換を行いました。この転換こそが、その後の「選択と集中」の経営へとつながっていきます。